Dargavel Village, Bishopton by BAE Systems
​
Shortlisted for Brownfield Awards Category 9 - Best Urban Regeneration /
Brownfield Scheme (Sponsored by AECOM)
Multidisciplinary team delivery of sustainable regeneration of a brownfield site or advancement and excellent implementation of a brownfield scheme with real positive economic, environmental and social impact.
Dargavel Village
​
The regeneration of the former Royal Ordnance Factory, Bishopton into the thriving mixed use development of Dargavel Village, is one of the largest brownfield projects in the UK, Figure 1 and 2. Dargavel Village is located approximately 15 miles from Glasgow. The former munitions and explosives manufacturing facility was initially constructed in 1909 for World War 1 and expanded for World War 2 and remained operational until 2001.
​
The 1,900 acre site is being sustainably transformed providing 4,000 new houses to create a place where housing neighbourhoods, greenspaces, community and commercial uses can be brought together in an integrated and co-ordinated way. Each stage of the Dargavel Village development has been planned and implemented in a manner sympathetic into the particular qualities of the location, and natural landscape features. Important to the success of the development has been the forging of durable links between the new and existing communities and providing a catalyst for wider regeneration via collaboration and engagement between stakeholders. Designed around village squares and green spaces and this major brownfield development supports the UK and the local long-term housing strategies with a high quality, sustainable and effective housing supply over twenty years.
​
The project is a multi-million pound programme funded and led by BAE Systems, where the remediation, construction, landscaping and ecological enhancement works are undertaken in a phased approach. Four of seven phases have been completed between 2012 and 2021, resulting in the transformation of 780 acres of brownfield land to date and the project concludes in 2034.
​
​
Project Achievements
​
To date, the project has included;
​
The site investigation, decontamination, demolition, remediation and earthworks of 460 acres of residential land and 320 acres of community woodland park, which has allowed construction and current occupations of approximately 1800 residential properties, Figure 2.
​
Provided 24 serviced development plots to housing developers through the construction of key spine infrastructure, including 4.5km of roads, two bridges and primary utilities; new M8 motorway junction 29a, rail connectivity, pumping stations, sustainable urban drainage solutions; flood compensation areas and 2km of river diversions, Figure 3. Commercial units have been built including a supermarket, local bar, dentist surgery and the Dargavel Village Primary School is in the advanced stages of construction, Figure 4.
​
Completed the construction and delivery of 8km of public accessible off-road path network and 250 acres of landscaped public green space, providing connectivity to the local countryside and linking residential areas, whilst promoting walking and cycling, Figure 5.
​
Created three acres of aquatic and wetland habitat; 200 acres of managed grassland; and nesting and breeding habitats for a range of fauna, including delivery of a long-term ecological monitoring and management plan.
​
Successful collaboration with numerous stakeholders, including the local authority Renfrewshire Council, SEPA, Nature Scot, HSE, NHBC, Considerate Constructors, statutory undertakers, existing Community Liaison Group, local resident groups and individuals, voluntary organisations, charity groups, developers and the local primary school. This approach has promoted highly collaborative working opportunities, innovative designs and enhanced outputs.
​
​
Remediation Summary
​
The phased environmental and geotechnical design appraisal as well as the remediation required was agreed with both Renfrewshire Council, SEPA and NHBC in consultation with the HSE.
​
Once the full scope of remediation and earthworks was established a process of re-evaluation and value engineering was implemented to maximise the environmental benefits, ensure the highest quality and ensure good value for money.
​
The ground investigation and remediation strategy is a ten stage process to address the industrial legacy is summarised as:
-
Decommissioning
-
Decontamination
-
Site assessment
-
Demolition
-
Hot spot removal
-
Environmental monitoring
-
Confidence scrape removal
-
Slab foundation and substructure removal
-
Bulk earthworks
-
Verification testing and sign off
​
​
Decommissioning & Decontamination: A programme of site wide building decommissioning occurred between 2001 and 2003. Detailed building inspections were undertaken to allow a decommissioning plan to be established and implemented. Bulk explosives that were identified were removed during the decommissioning phase via thermal treatment, ex-situ bio-remediation and bespoke techniques.
​
Following the decommissioning works a programme of decontamination was completed between 2011 and 2013 and involved a combination of HSE approved methods to reduce the risks by way of thermal treatment and high pressure cleansing of buildings and materials.
​
Site Assessment, Hot Spot Removal & Verification: A preliminary risk assessment for land contamination was completed and site investigations have been ongoing on a Land Quality Management Area (LQMA) basis where the Site was subdivided into 42 discrete LQMAs to allow site works to be effectively managed. Extensive soil and water sampling to characterise ground conditions and potential sources of contamination has included 15,000 soil and 4,000 water samples analysed for key contaminants of concern.
​
A very comprehensive three tiered sampling verification strategy was approved to demonstrate satisfactory remediation.
-
Tier 1 – Hot spot removal.
-
Tier 2 – Soil characterisation and 25m intermediate verification grid (IVG) prior to confidence scrape and earthworks.
-
Tier 3 – Final verification grid (25m off-set 12.5m from IVG) following completion of earthworks.
​
A precautionary remedial approach is adopted at each tier and where results are indicated to exceed at an isolated grid point, a remedial excavation occurs centred on the hot spot with five subsequent verification samples. Where adjacent 25m grid points fail the remediation criteria for the same determinands, this triggered excavation halfway to the nearest grid sample point which passed the criteria.
​
Demolition & Substructure Removal: The works include demolition and foundation removals of 770 buildings with 95% of the materials being re-used including 100,000 tonnes of brick and 190,000 tonnes of concrete and value recovery achieved from the recycling of 19,000 tonnes of scrap metal.
​
Confidence Scrape: One of the key remedial actions is confidence scraping across the entire core development area to a minimum depth of 0.15m of near surface soft deposits considered as the likely source for spills and leaks from explosives propellant and conventional contaminants. Approximately 350,000m3 of soil is reused to construct landscape mound and/or restore the borrow pit where glacial till was extracted as fill for development plots.
​
Bulk Earthworks: Significant earthworks operations have involved movement of 1.3 million tonnes of material to re-profile the topography of development platforms achieving an earthworks balance and mitigating the need to import or export soils from the Site.
​
Compliance with Legislation, Codes and Guidance
​
The success of the project is underpinned by very strong stakeholder engagement and the excellent relationships forged with all works carried out in strict accordance with legislation and best industry guidance.
​
The discharge of the three planning conditions by Renfrewshire Council are key and specific to the Site Investigation, Remediation Method Statement and a Verification Report to allow development.
​
In addition, Land Quality Endorsement from the NHBC was achieved in relation to more recent plots and the HSE routinely approves amendments to reduce the explosives licence boundary following remediation. The following regulatory authorisations, licences and accreditation certificates have been acquired and maintained by BAE Systems:
​
-
Environmental Management System ISO 14001:2015.
-
Quality Management System ISO 9001:2015.
-
Waste Management Licence – Mobile Plant: SEPA.
-
Scottish Landfill Tax, Revenue Scotland.
-
Landfill Construction and Operation: Pollution Prevention and Control SEPA.
-
Association of Geotechnical and Geo-environmental Specialists (AGS): Certificate of Membership (2020).
-
Explosives Licence: HSE.
-
Ecological Licences: Badgers, Birds, Otters: NatureScot
-
Craigton Burn Works Licence: SEPA.
-
Cordite Burn Works Licence: SEPA.
-
Construction Site Licence: SEPA.
​
​
Health, Safety & Environmental Challenges
​
Bulk Explosives: The identification, removal and disposal of explosive materials, products and residues represents a key safety critical element of the programme. Leveraging subject matter expertise to develop techniques and safe systems of work to reduce the risks to site workers and future material usage, by the early and phased removal of bulk explosive and products.
​
Detailed investigation and characterisation of individual production buildings and the potential risks allowed bespoke decontamination solutions to be developed and implemented for each structure and area of the site. Incorporating remote working, thermal treatment techniques, high pressure water cleansing and controlled excavation has allowed the certification of buildings and arisings such as scrap metal as ‘Free from Explosive’.
​
Soil Movements & Waste: The success and credibility of remediation depends on the ability to provide clear and auditable tracking of materials movements. SEPA commented on the exemplar materials management and live tracking achieved by the electronic tracking for every load of soil, Figure 6. This has resulted in the ability to reconcile material movements and provide accurate evidence in demonstrating compliance with the regulatory agreed strategies, maximising soil reuse and minimising importation or off-site deposition.
​
A mobile plant waste treatment hub allowed the waste hierarchy to be implemented where soil was mechanically, screened and segregated and subjected to further testing. This allowed more soils to be reused and minimised sentencing of waste to the on-site PPC regulated stable non-reactive non-hazardous waste landfill. Soil not suitable to remain within the core development area was either re-used to construct landscape mounds within the country park or entered the waste stream and retained in the onsite landfill.
​
Silt Management: The potential to cause pollution to the water environment via silt run-off to water courses is an ongoing challenge which is tightly managed in accordance with the guiding principles set out within the Site Wide Pollution Prevention Plan and individual remediation phase plans submitted and approved by SEPA under the Construction Site Licence.
​
River Diversions and Flood Assessment: The re-alignment of approximately 2km of surface water channels including the Craigton and Cordite Burns and the construction of a cascade waterfall overcame the topographical challenge and has significantly improved the quality and public amenity of the sites water network, which was previously culverted below ground during factory operations. This created a carefully designed landscape feature within the development’s green spaces, in addition providing and enhancing habitat for protected wildlife.
​
Surface water modelling and flood risk assessment allowed innovative design to mitigate the need for a flood compensation storage area and heavy engineering within a natural surface water and long term management requirements. The solution included land lowering adjacent to the water course and installation of meanders into the channel including bridge narrowing to achieve surface water throttle.
​
Ecology: Ecology management across the programme is led by a dedicated ecological team integrated at all stages of the redevelopment, from planning and design to site implementation. Currently in place for ten years, this approach has mitigated impacts to existing ecology, provided a focus and knowledge base to leverage ecological improvements in attracting greater species diversity within the development.
​
To date, ecological mitigation and enhancement undertaken on the site comprises the construction of three acres of aquatic wetland habitat; installation of bat, barn owl, stock dove boxes; construction of three artificial badger setts; installation of badger tunnels beneath new road infrastructure; construction of two artificial otter holts and use of amphibian kerbs, created in line with best practice guidance.
​
The long-term scheme has also presented opportunities for innovative and creative solutions to improve habitats for protected species. E.g. the construction of a barn owl tower utilising 95% recycled construction materials and the creation of features to encourage species not yet recorded on site, but whose ranges are expanding in the local area. These include osprey nesting platforms and pine marten boxes.
​
Landscaping and Amenity
​
Landscaping works are designed to improve habitats, protecting and enhance existing ecology. Engineered features such as new river channels facilitate public access whilst mitigating disturbance to existing ecology. The creation of village square green spaces with wild flower meadow areas provides habitat for insects, bats, birds and small mammals. The installation of features such as factory monument which was designed to capture the sun setting on the 11th November each year, installed to commemorate the World War centenary and ensures the historical significance of the former factory and the contribution of the local communities is maintained.
​
Viewing points encourage local residents to explore outdoors, provides focal points and a sense of place within the development. Play parks have also been incorporated within the green areas providing further public amenity. Tree planting across the landscaped areas utilises a native tree mix, approximately 25,000 trees have been planted to date through green spaces.

Figure 1: Master Plan

Figure 2: 1800 Residential Homes
​
Aerial view from left to right, completed residential areas, remediated development plots, remediation in progress.

Figure 3 – M8 Motorway Junction 29a and railway bridge
Key transport link to existing infrastructure
Brownfield regeneration enables new primary school facility

Figure 4 – Dargavel Primary School
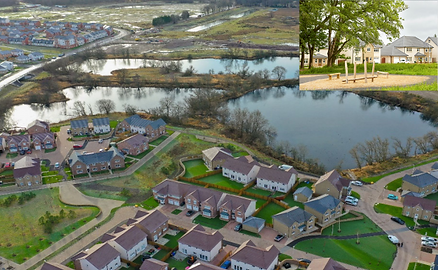
Figure 5 – Dargavel Village Public Open Space
Public open space links residential areas, ecological habitats and green corridors
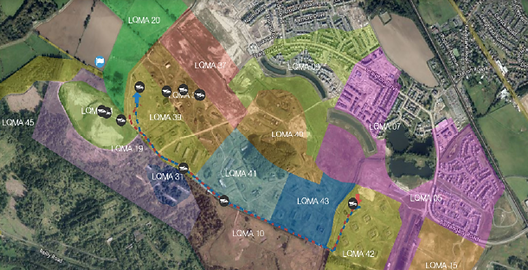
Figure 6 – Real Time Materials Tracking
Extract of materials tracking software